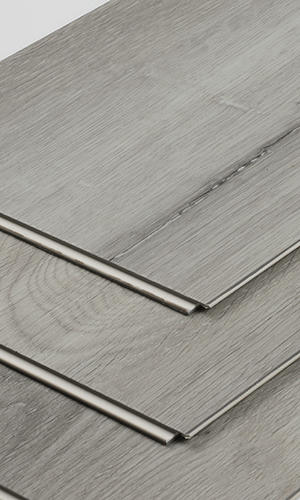
Luxury Vinyl Tile is a composite product that has multiple layers working together to create a resilient, low-maintenance flooring. The bottom layer is a backer board that is flexible and made of PVC for stability. The central core is water-resistant and gives the flooring its strength, while the top layer is the decorative vinyl film that is printed with the design – traditionally mimicking wood or stone. The clear vinyl layer allows for a wide range of designs and patterns that make the finished product extremely versatile.
The manufacturing process starts with blending raw materials to make an evenly blended, consistent compound. This is then fed into a calendering machine that works the compounds through heated rollers that compress and form it into a sheet. Once formed, it is then sent through a cooling section before lamination.
At this point the manufacturer can add any desired textures and embossing to the floor. Some of the higher end brands will even include an aluminum oxide coating to help protect the floors from stains and scratches. The final step is adding the protective urethane wear layer. This is what really makes the difference and determines how long your new floor will last before it needs to be replaced. Ideally the wear layer is about 20 mil thick, although some manufacturers offer products with a much higher wear layer for commercial applications.
LVT flooring is available in loose lay and click formats. Loose lay LVT is very similar to laminate in that it can be installed without the use of adhesives, though manufacturers recommend a full spread of adhesive around the perimeter for large rooms. For smaller spaces and rolling loads, the loose lay versions can be clicked together to lock them in place.
Some manufacturers are offering slightly more adventurous options by not attempting to replicate the appearance of natural materials, instead they are taking an artistic approach with geometric and graphic prints that create an almost abstract effect on the floor. This is an exciting development and we expect to see more of these unique options becoming available as the market grows.